アクリル加工虎の巻
今ではアクリルの板材や、専用の工具などもホームセンターやネットショップで気軽に購入できるようになった為、DIYでご自分で加工をなさる方も多くアクリルという素材が身近な材料になってきています。
少し難しい感じがあるアクリル加工ですが、アクリルの特性やコツがわかれば、面白い効果や綺麗な加工が出来る魅力的な材料です。
ここではアクリルの特性や加工のコツ等をご紹介。アイデアを形にするヒントとしてお使い下さい。
アクリルクラック実験
”クラック” -聞き慣れない言葉だと思います。
プラスチック材料を扱っている方が聞くと嫌な単語です。
これはプラスチックに起こるひび割れの事なんです。
高い所からドカンと落とすと入るヒビはもちろんですが、プラスチックは化学製品なので科学的作用や熱作用等で組織が壊れてヒビが入ってしまう事があるんです。
通常クラックが入った製品は失敗(不良)という事で製品にはならないので、世に出る事はありません。
そんなアクリル業界では忌々しい”クラック”。
今回はこの世に出ないクラックを意図的に出してみます。
アクリルのクラックを意図的に起こしてその偶然性から何かできないか?そこで何が分かるのか?果たして製品として使えるか?を検証してみたいと思います。
アクリルクラック大実験、これを行うにはまずアクリル板材におけるある知識を知らなければいけません。
それはアクリル板材には作り方の違いがあるという事。
つまり一見同じアクリル板でも作り方によって特性が変わってきてしまうのです。
違いは大きく分けて2つ。「押し出し材とキャスト材」です。実験をする上で2つの材料の違いを見る必要があります。
まず「キャスト材」
歴史は古く、かの昔はこの材料しかありませんでした。
平行を出す為2枚のガラス板の間に溶けたプラスチックを流し込み板にした物、ぎゅっと密度の詰まった板なので固く、熱にも強い。
パーフェクトなアクリルなのですが、値段が高い事、板厚寸法が一定ではない事といったデメリットもあるのです。
対して「押出し材」
名前の通りプラスチック樹脂をローラーで押出て板を作ります。大量生産が出来る為安い!そして板厚寸法がばっちり出ています。
しかしキャスト材に比べると樹脂の密度が粗いので熱には少し弱め。
でもどちらも外観的には、ほぼ一緒なので一般的なアクリル板製品は押出材がほとんどです。
以上を踏まえて今回は5種の材料を用意しました。
一般的な材料と特殊な材料織り交ぜています。
①アクリル押出し 透明 5mm(一般的にアクリル什器に使われるちょっと厚めの板)
②アクリルキャスト クリアパープル 5mm(キャスト材の高級路線、特殊色です)
③アクリル押出し 透明 3mm(アクリル什器に最も使われている板厚3mm)
④アクリル押出し 透明 2mm(少し薄めの板厚2mm)
⑤アクリル押出し エッジカラーパープル 3mm(押出材の特殊色、切った部分が色付きに光るエッジカラー)
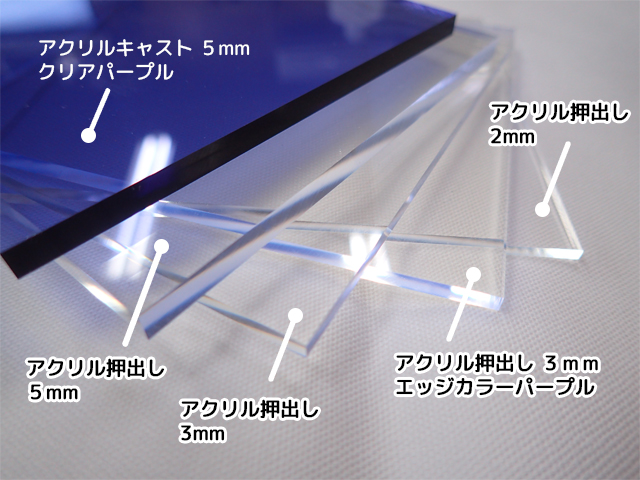
実験方法
クラックが起こる原因は大きく分けて2つ薬品による化学変化と熱による変化があり「薬品による化学変化」と「熱による変化(温めた後、急激に冷ます等)」の2つ
今回は再現度の高さとクラック後に何か加工が出来る事を条件として、
「熱による変化」
この方法を選んでクラックを起こしてみようと思います。
今回は大きくクラックを出したい為、各材料の端面をバーナーで炙り、その後すぐにアルコール系の溶剤に漬けてふき取ります。
熱した材料が急激に冷まされる事でクラックを出してみよう!という試みです。
バーナーの炙り加減は1秒間に2センチ程度移動させるスピード、板の端面が熱で溶ける手前ぐらいの炙り加減。
アルコール溶剤はイソプロピルアルコールを使用。
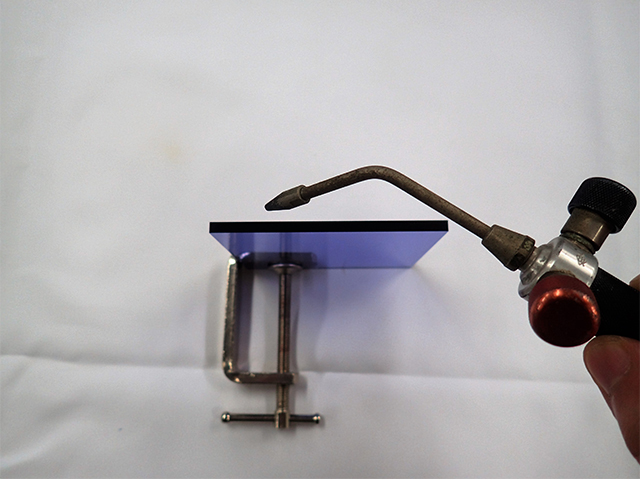
炙り字の熱の加わりかたでクラックの出方が変わってしまう事を想定して、各4辺同じような方法でクラックを出して出方を検証。
そして材料ごとの違いを見てみよう!というねらいです。
①キャストと押出のクラック検証板厚5mm
5㎜の押出とキャストの比較です。
クラックがあまり出ていません!
押出は若干ヒビが入った程度なのですがキャストは本当にほんのりです。
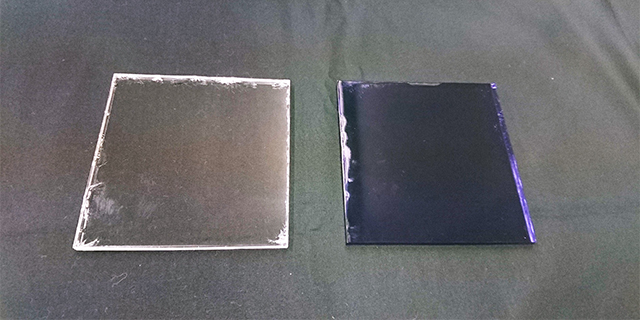
キャスト材のアップです。
材料の中にほんの少しのヒビが見えます。
実験的にはあまり良い結果ではなかったのですが逆を言えばキャスト材の強度がそれだけ良かったという事が言えるのかもしれませんね。
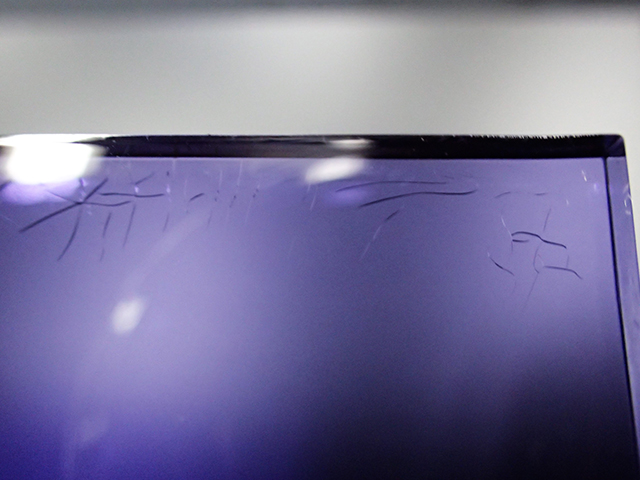
②押出3mmのクラックの出方とエッジカラーはクラックでどうなるか?
続いて3㎜の押し出し材の透明とエッジカラー材比較です。
どうでしょうか。5mmと違い良い感じにクラックが出ていますね。
ただ、炙りのむらのせいかクラックもむらが見えますね。
エッジカラー材ですが、クラックの形状も面白い形状が出ています。
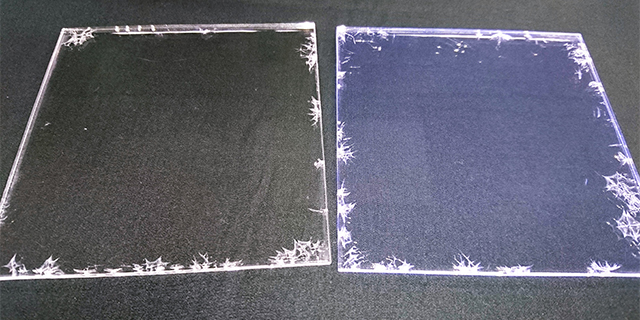
エッジカラー材のアップです。
蜘蛛の巣状のクラックが出ています。
写真ではわかりにくいですが、ヒビの部分もエッジカラーの特性である切り口に色が付くというのは生きていてレーザー彫刻に近い感じが出ています。
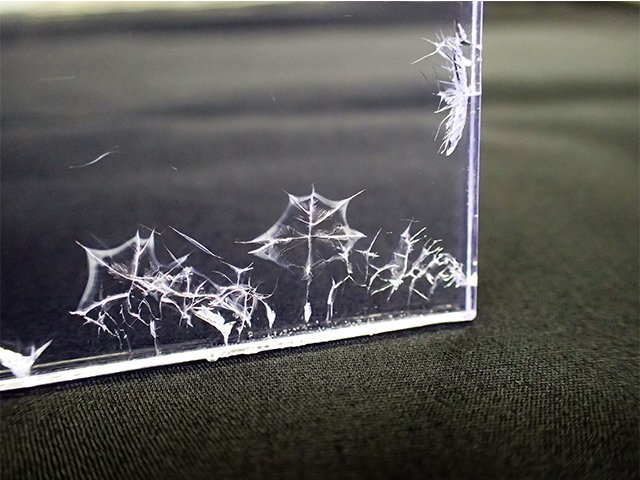
③押出2mmのクラックの出方
2㎜材です。
これはかなりのクラックが出たのではないでしょうか。
やはりむら感は否めないですが、思っていたクラックに一番近い状態が出ている気がします。
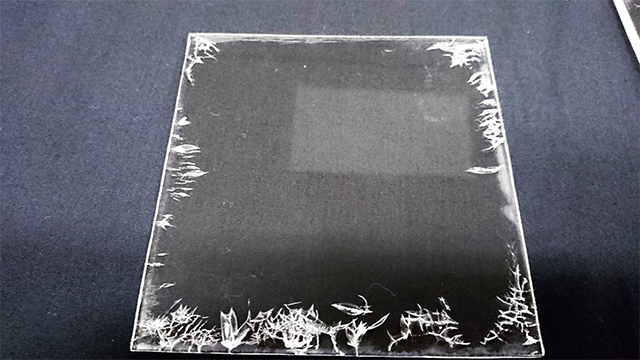
一番クラックの大きかった2㎜のアップです。
クラックに加えて白化が見られます。
あまり綺麗では無いのですがこの白化は拭いても取れないので、バフ等の2次加工でとる必要がありますね。
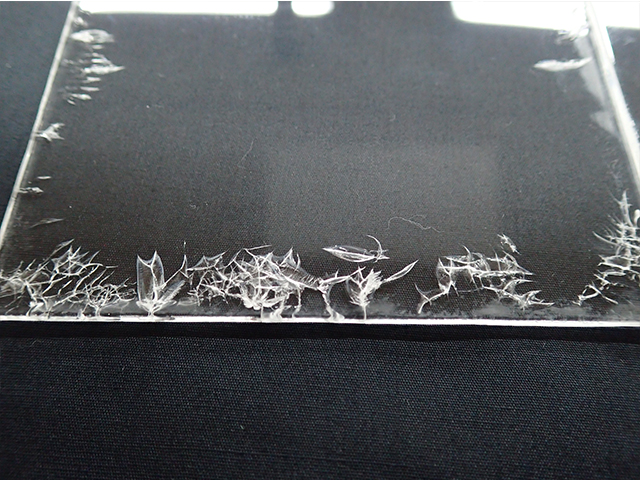
押出材シリーズの比較です。
右から5㎜・3㎜・2㎜となっています。
やはり熱の伝わり方がネックなようで板厚が薄い程クラックの出方や細かさが大きいという事が分かりますね。
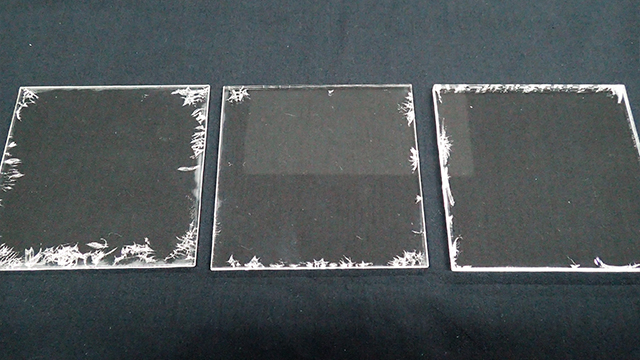
さて、次は2mm板をさらに強引にクラックを出していき今度はエッジだけではなく全面的に炙って板のソリや熱変形は関係なく、
どれだけクラックを出せるか。
そしてその状態の物が、製品として、また表現として見せれる物になるかという追実験をしてみます。
さて、実験結果。
これです、板はもう平行度はありません。そして白化も凄いです。
拭いても拭いてもこの感じです。
しかし、今回はクラックを見せる物への実験なので、白化した部分をバフで磨き透明度を取り戻します。
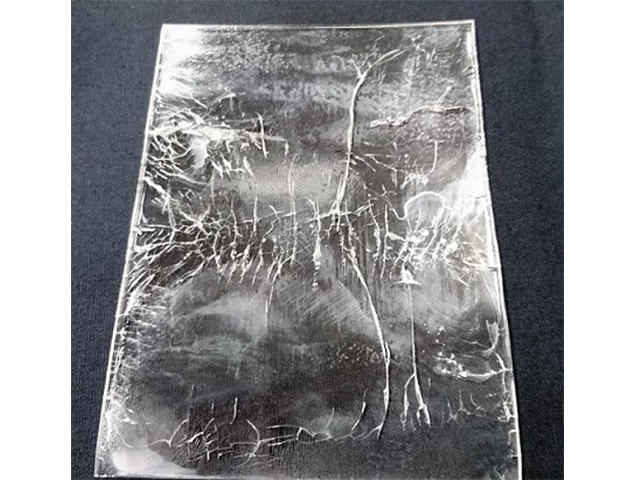
バフ加工後ここまで綺麗になりました。
白化は全て取り除いたのですが、写真中央と右側、少し曇っていますよね。これは白化とは違う現象でした。
ここをアップにしたいと思います。
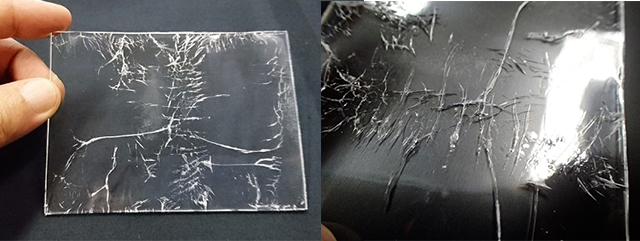
まず中央部何か細かいクラックが幾何学模様のようになっていますね。
エッジ側はこんな感じ。アップで見るとちょっとアートな感じに見えなくもないのですが材料的に曇った感じになるので面白い効果ではあるのですが、見た目は正直綺麗ではないです。
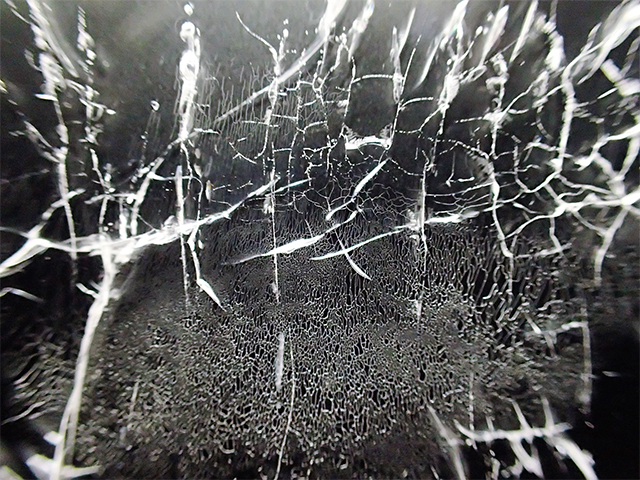
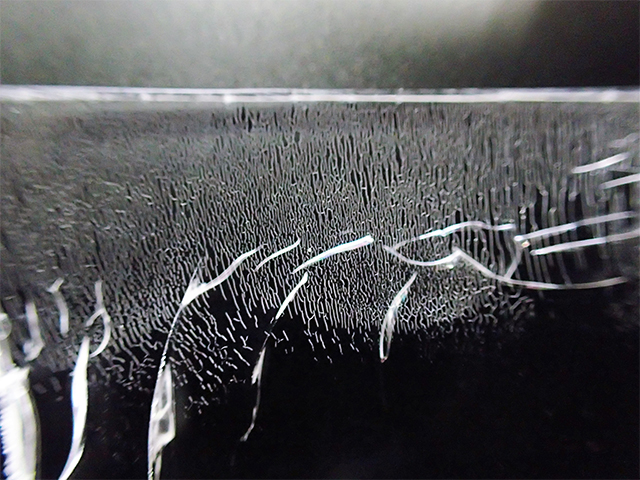
今回の熱による実験では熱なので、バーナーではなくホットプレートでどうなるか、レーザーではどうか等もっと広げた実験やアルコール溶剤を変えてみる等実験条件の細かな設定も行わずいきあたりばったりな実験だったのですが、他にはあまり無いデータが出たような気がします。
そしてクラックと同時に板の白化が発生して場合によっては汚いと感じる割れになる事が分かりました。
では、これを製品にできるのか?という疑問ですが、偶然の産物といった所で板厚の違いで綺麗に(外観的に沢山)クラックを出すには熱量が必要な事と、熱を加えすぎると板が溶けてくるという狭間で板を綺麗な状態のまま大きなクラックを出すのは難しいという事で生産性といった所ではまだまだ改善の必要があります。
クラックの形状によっては面白い形の物も多く、クラックのコントロールがある程度可能になった場合、アイデアにマッチ出来るような効果が生まれる可能性は大きいです。
クラックの味を生かしさらに製品化というのであれば、例えば写真フレーム等でエッジのみのクラックを生かしてオールド感や壊れ感を出す等ぐらいが限界かな?と感じていますが、アイデアがあれば何か用途があるかもしれません。